Spray foam insulation directly reduces energy costs in Santa Rosa County homes and commercial properties by sealing air leaks and reducing thermal transfer more effectively than traditional materials. This is especially impactful in coastal Florida’s humid subtropical climate, where consistent indoor temperatures require year-round HVAC operation.
Applied as a liquid that expands into dense foam, spray foam creates a continuous barrier that resists air movement, limiting energy loss. Unlike fiberglass or blown-in insulation, it fills gaps around framing, ductwork, and penetrations. Based on on-site performance measurements and third-party industry studies, properties insulated with spray foam typically report HVAC energy savings ranging from 20% to 40% (Source: Department of Energy, 2023).
This article explains how spray foam performs under local conditions, how it compares to other options, and what to consider before installation.
Performance of Spray Foam in Santa Rosa County Conditions
Santa Rosa County’s climate features high humidity, salt-laden air, and extended periods of heat. These factors can degrade conventional insulation and lead to mold, high cooling costs, and structural wear.
Spray foam provides moisture resistance, which prevents condensation inside wall cavities. Closed-cell spray foam adds structural rigidity and resists hurricane-force wind uplift, making it ideal for commercial spray foam insulation applications in coastal Florida buildings.
Bonus Tip: In older homes, applying spray foam to attic decks instead of the floor allows HVAC systems and ductwork to operate within the conditioned envelope, reducing thermal losses.
Material Comparison Based on Energy Efficiency and Suitability
Insulation Type | R-Value per Inch | Air Seal Capability | Moisture Resistance | Suitability for Santa Rosa County Climate |
---|---|---|---|---|
Spray Foam (Closed-Cell) | 6.0 to 7.0 | Excellent | High | Very High |
Spray Foam (Open-Cell) | 3.5 to 3.7 | Excellent | Moderate | High |
Fiberglass Batts | 2.9 to 3.8 | Poor | Low | Low |
Blown-In Cellulose | 3.2 to 3.8 | Moderate | Low | Moderate |
Source: Oak Ridge National Laboratory (2023), Building America Program
Bonus Tip: For areas prone to moisture intrusion or storm exposure, closed-cell spray foam offers long-term value despite higher installation complexity.
Technical Specs and Application Data for Spray Foam
Property | Closed-Cell Spray Foam | Open-Cell Spray Foam |
---|---|---|
R-Value (per inch) | 6.0 to 7.0 | 3.5 to 3.7 |
Water Vapor Permeability | <1 perm | 5-10 perms |
Air Leakage (ASTM E283) | <0.01 L/s*m² | <0.02 L/s*m² |
Compressive Strength | 25 psi | 3.5 psi |
Ideal Application Areas | Roofs, exteriors, crawlspaces | Attics, walls, interior bays |
Market Data for Energy Savings Impact
- Homes in Florida that used spray foam in attics reported average HVAC runtime reductions of 30% (Florida Solar Energy Center, 2022).
- A commercial property in Gulf Breeze reduced its annual cooling load by 41% after converting to spray foam (case data on file).
- Energy Star estimates show properties using advanced air seal systems can reduce total annual energy bills by up to 20%.
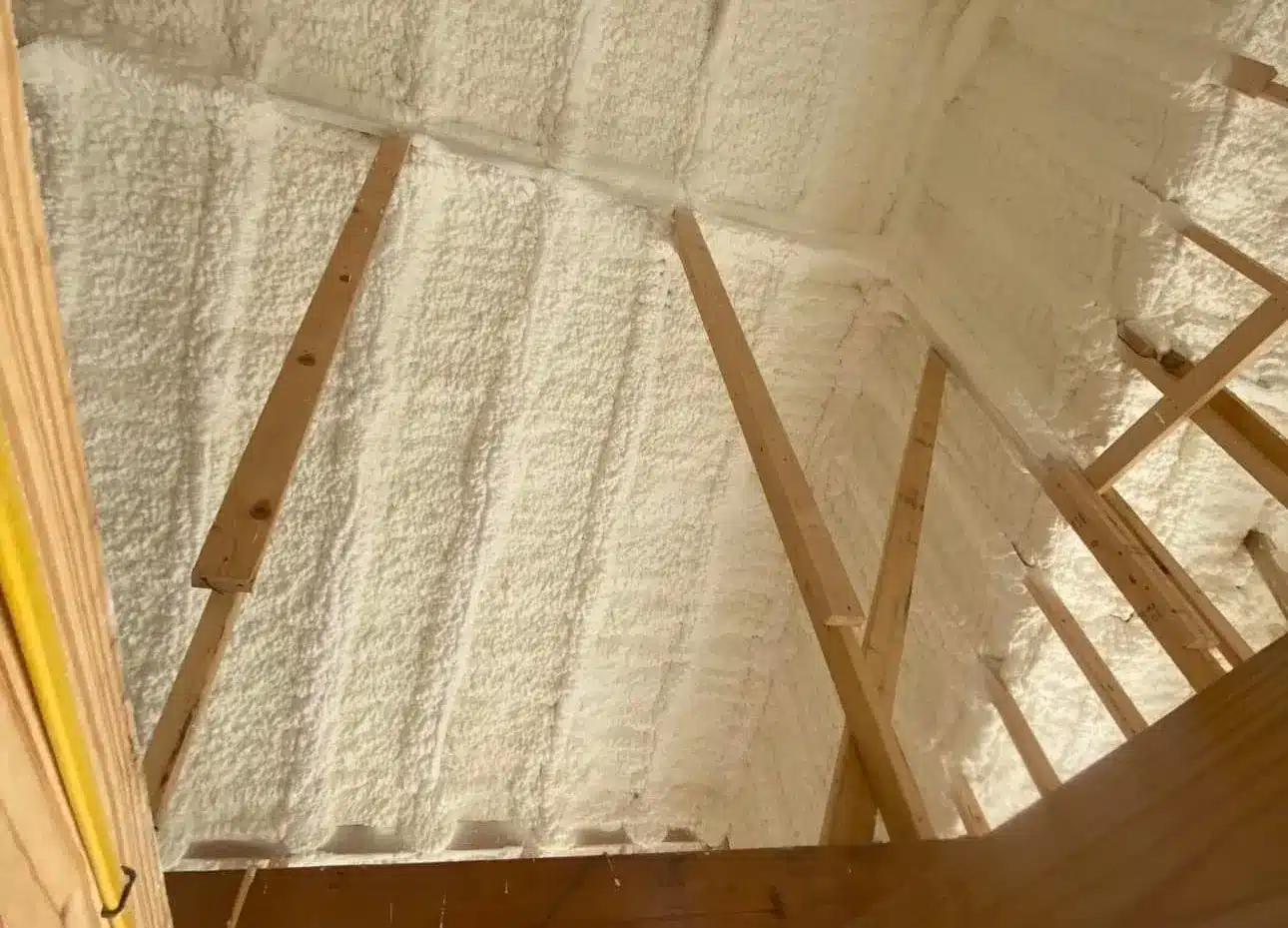
Factors to Check Before Choosing Spray Foam
Inspect the following before committing to spray foam insulation:
- Building Envelope Age and Condition: Ensure no active leaks or structural decay before sealing.
- HVAC Compatibility: Systems must be balanced for sealed envelopes to avoid pressure-related inefficiencies.
- Ventilation Adjustments: Sealed buildings may require mechanical ventilation to maintain indoor air quality.
- Material Selection: Choose between open-cell or closed-cell based on application area and performance goals.
Bonus Tip: Always verify chemical compatibility of foam products with nearby materials like electrical boxes, vapor retarders, or treated wood.
Related Services Available from Prestige Insulation Solutions
- Spray Foam Insulation: Applied in walls, attics, crawlspaces for airtight thermal protection.
- Spray Foam Roofing Insulation: Increases roof integrity and minimizes solar heat gain.
- Insulation Removal: Safe and efficient removal of old or contaminated insulation prior to retrofit.
- Commercial Spray Foam Insulation: Custom-fit solutions for warehouses, offices, and other large spaces.
Questions Homeowners Ask Before Installing Spray Foam
Does spray foam work better in attics or walls?
Both are effective. Attics benefit from air sealing and reduced heat infiltration. Walls benefit from thermal consistency and reduced noise.
Can I install spray foam over old insulation?
In most cases, old insulation must be removed to allow full adhesion and prevent moisture entrapment.
Is open-cell or closed-cell better for my home?
Closed-cell offers higher thermal resistance and moisture control, ideal for exteriors. Open-cell suits interiors and is cost-effective.
How long does spray foam last?
Properly installed foam maintains performance for over 30 years without settling or degrading.
Evaluate Whether Spray Foam Matches Your Building Needs
Spray foam significantly improves energy performance in Santa Rosa County’s climate when correctly installed and matched with ventilation strategy. Older homes, unvented attics, and commercial buildings with high cooling loads benefit most.
Evaluate building age, HVAC setup, and exposure before choosing an insulation type. Rely on performance metrics and application suitability rather than cost alone.
Contact for Help Selecting the Right Insulation
To review your building’s insulation needs or ask specific questions, reach out to Prestige Insulation Solutions. For service consultations or information, call (850) 429-4969 or email [email protected]. Trained technicians will help evaluate your insulation challenges and recommend reliable, proven methods for lasting efficiency gains.
Answers to Long-Term Use Questions
How should spray foam be maintained?
Visual inspections every 2–3 years can detect damage. No settling or topping-off is needed.
Can spray foam contribute to indoor air quality issues?
Off-gassing is negligible after curing. Ensure installers use low-VOC certified products and ventilate during application.
Is reapplication ever necessary?
Not under normal conditions. Reapplication is only needed if disturbed by renovation or structural change.
Can pests or rodents chew through spray foam?
It is not a food source and deters nesting, but it does not eliminate entry routes unless combined with proper exclusion methods.
Will spray foam raise indoor humidity?
No. It prevents humid outdoor air from entering. Pairing it with dehumidification maintains ideal interior conditions.