Blown-in insulation becomes necessary when a home exhibits uneven temperatures, escalating energy bills, or persistent drafts. These issues signal insufficient thermal resistance, often in attics or wall cavities. Blown-in materials fill irregular spaces effectively, reducing heat transfer and improving indoor comfort.
In climates with high humidity and fluctuating temperatures, like the Gulf Coast, insufficient insulation contributes to condensation, mold, and premature HVAC wear. Identifying key symptoms early avoids structural deterioration and stabilizes energy use. This article outlines practical signs and technical indicators that suggest the need for blown-in insulation.
Observable Signs of Inadequate Insulation
Temperature Variation Between Rooms
Consistent temperature differences between floors or rooms point to compromised insulation. Blown-in materials evenly distribute coverage in cavities, resolving thermal gaps.
Increasing Energy Consumption
If heating or cooling demands rise without lifestyle changes, insulation performance may be declining. Blown-in cellulose or fiberglass can restore resistance levels.
Frequent HVAC Cycling
When systems activate repeatedly, they compensate for temperature loss. Improved insulation slows thermal exchange and reduces system stress.
Ice Dams in Cold Weather
Accumulated ice near roof edges suggests rising heat through poorly insulated attic floors. Blown-in material helps create a uniform thermal barrier.
Moisture Accumulation and Mold
Poorly insulated attics trap moisture in sheathing. Blown-in insulation creates more effective seals around rafters and penetrations.
Comparison of Insulation Methods
Feature/Criteria | Blown-In Insulation | Batt Insulation | Spray Foam Insulation |
---|---|---|---|
Air Gap Coverage | Excellent (fills cavities) | Moderate (cut-to-fit) | Excellent (expands on contact) |
Installation Time | Fast | Moderate | Moderate |
Settling Over Time | Moderate | Low | Low |
Sound Dampening | Good | Fair | Excellent |
Wall and Retrofit Access | High | Low | Moderate |
Recommended for Retrofits | Yes | No | Sometimes |
Material Types Used | Cellulose, Fiberglass | Fiberglass | Polyurethane |
Technical Performance Data
Metric | Blown-In Cellulose | Blown-In Fiberglass |
---|---|---|
R-Value per Inch | R-3.2 to R-3.8 | R-2.2 to R-2.7 |
Moisture Resistance | Moderate | High |
Fire Resistance (Treated) | Yes | Yes |
Material Density (lbs/ft³) | 1.5 – 3.0 | 0.5 – 1.0 |
Settling Rate (Over Time) | 13-20% | <5% |
Factors to Evaluate Before Choosing Blown-In Insulation
Access and Structural Gaps
Evaluate wall cavities, attic joists, and floor structures. Blown-in insulation is ideal for enclosed, hard-to-reach areas without requiring major structural alterations.
Material Compatibility
Verify whether cellulose or fiberglass fits existing construction materials. Cellulose suits older homes; fiberglass works better in moisture-prone areas.
Local Climate Considerations
In humid regions like northern Florida, fiberglass’s resistance to moisture absorption may offer longer performance stability.
Bonus Tip
Before installation, seal attic penetrations and light fixtures. Air sealing enhances the effectiveness of blown-in insulation.
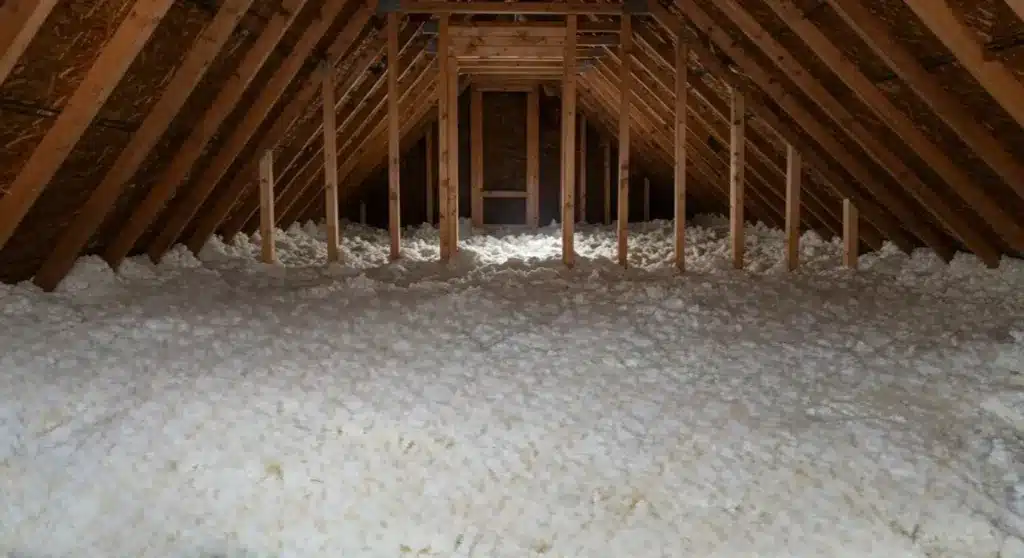
Closely Related Services Offered by Prestige Insulation Solutions
- Blown-In Insulation Fills wall cavities and attic floors with minimal disruption, increasing efficiency and comfort.
- Insulation Removal Safely extracts outdated or damaged insulation to prepare for a new installation.
- Roof Insulation Enhances resistance across pitched and flat roofing systems, reducing attic heat gain.
- Spray Foam Roofing Insulation Provides a seamless thermal envelope for roof decks, reducing air leakage.
Immediate Questions Homeowners Ask
How long does blown-in insulation last?
Most blown-in materials, when installed correctly, maintain performance for 20–30 years. Settling may occur, but density and R-value remain effective if undisturbed.
Can blown-in insulation be added over existing material?
Yes, it can supplement existing fiberglass batts or other types if the current insulation is dry and mold-free.
Does it make a mess during installation?
Minimal disruption occurs if applied by experienced crews using vacuum systems and targeted hoses.
Is cellulose better than fiberglass?
Cellulose offers higher R-values per inch and eco-friendliness. Fiberglass has better moisture resistance. Choice depends on structure and region.
Summary of What to Look For
Temperature inconsistency, increased energy use, visible moisture, and system overuse are direct signs that insulation is underperforming. Blown-in insulation addresses these efficiently in enclosed or irregular cavities. Choosing the right material based on regional climate and building type ensures lasting impact.
Contact for Next Steps
For insulation upgrades backed by tested field experience, contact Prestige Insulation Solutions at (850) 429-4969 or email [email protected]. Trained crews assess conditions, recommend viable solutions, and ensure clean, efficient execution without disrupting daily life.
Long-Term Considerations and Maintenance
How often should insulation be inspected?
Attics and wall cavities should be inspected every 5–7 years to identify settling, rodent activity, or moisture intrusion.
Can blown-in insulation attract pests?
Untreated cellulose may. However, modern materials are treated with borate, which resists insects and rodents.
Will it reduce external noise?
Yes. Denser blown-in materials fill gaps that carry airborne sound, offering moderate noise dampening.
What happens if water damage occurs?
Wet insulation loses effectiveness. Immediate removal and replacement are recommended to avoid mold and structural damage.
Is it safe for people with allergies?
Fiberglass is less likely to hold allergens. Encapsulation methods and proper sealing reduce risk for sensitive individuals.