Blown-in insulation can be effective for Fort Walton homes when air retention, attic coverage, and retrofit adaptability are priorities. Its ability to fill irregular cavities and existing wall spaces makes it practical for older homes needing insulation upgrades. Fort Walton’s humid subtropical climate increases the need for materials that resist moisture without trapping it, and blown-in insulation performs moderately well in this regard.
Compared to batt insulation, blown-in insulation provides more complete coverage, reducing air leaks in attic floors and wall cavities. However, it lacks the air-sealing capacity of closed-cell spray foam. For homes with frequent temperature swings and high humidity levels, additional vapor barrier measures may be necessary.
Performance Traits of Blown-In Insulation in Fort Walton Conditions
Regional Suitability
Fort Walton experiences long, humid summers and mild winters. Roof and attic insulation play a significant role in indoor comfort and HVAC efficiency.
- Humidity Management: Blown-in cellulose retains moisture more than fiberglass. In unvented attics, this can reduce long-term performance.
- Air Movement: Loose-fill blown-in materials slow but do not block air transfer. Supplementary sealing may be required in high-humidity zones.
- Retrofit Efficiency: Ideal for upgrading insulation in existing walls without major renovations.
Material Comparisons
Material Type | R-Value per Inch | Moisture Sensitivity | Settling Over Time | Air Sealing Capacity | Fire Resistance |
---|---|---|---|---|---|
Blown-In Fiberglass | 2.2 – 2.7 | Low | Low | Low | Moderate |
Blown-In Cellulose | 3.2 – 3.8 | Moderate | High | Low | High (treated) |
Closed-Cell Spray Foam | 6.5 – 7.0 | Very Low | None | High | High |
Bonus Tip: Blown-in fiberglass is often preferred in coastal climates due to lower moisture absorption compared to cellulose.
Installation Considerations and Practical Specs
Installation technique affects thermal performance, durability, and inspection accessibility. Dense-pack wall insulation requires specialized equipment to avoid underfilling or voids.
Installation Factor | Best Practice | Risk if Ignored |
---|---|---|
Attic Depth | Achieve consistent 13-15 inches | Uneven insulation leads to heat pockets |
Air Leakage Control | Pair with air sealing measures | Higher energy costs due to drafts |
Soffit Vent Clearance | Maintain baffles at eaves | Moisture buildup and reduced airflow |
Existing Wall Retrofits | Dense-pack technique recommended | Voids reduce effective R-value |
Bonus Tip: For homes near the Gulf Coast, using vapor-permeable netting during wall fill prevents moisture buildup without trapping it inside cavities.
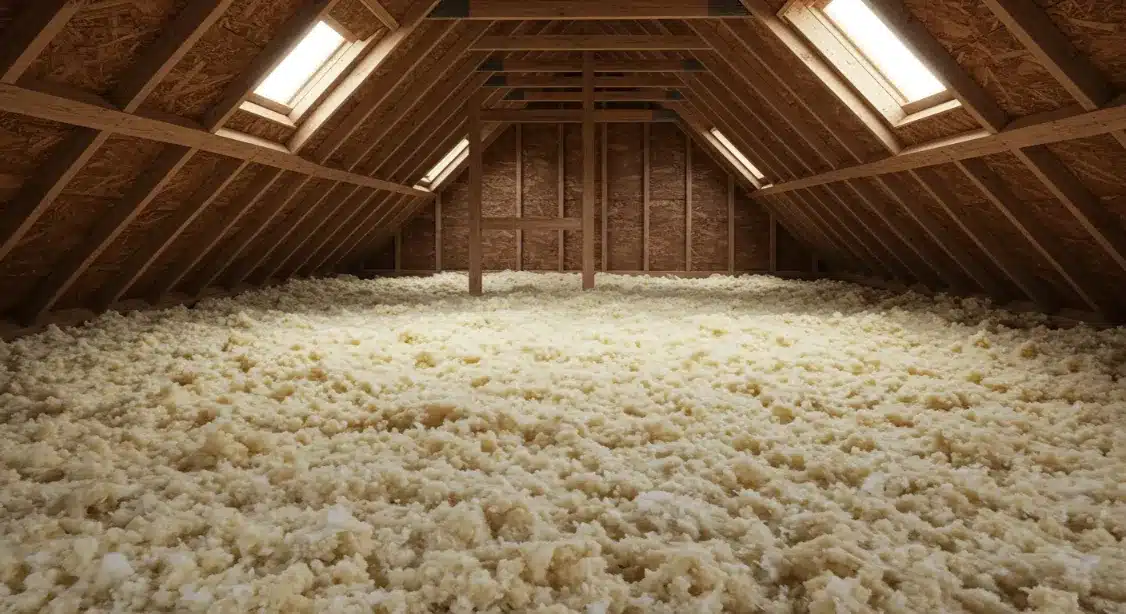
Things to Check Before Choosing Blown-In Insulation
- Attic Ventilation: Poor airflow may reduce insulation effectiveness. Verify soffit and ridge vent operation.
- Roof Deck Integrity: Insulation won’t correct roofing issues. Check for leaks or warping.
- Pest Activity: Loose-fill can conceal rodent activity. Inspect for droppings or nesting signs beforehand.
- Electrical Safety: Knob-and-tube wiring is incompatible. Confirm compliance with modern electrical codes.
Common Questions Before Installing Blown-In Insulation
How long does blown-in insulation last?
Up to 20–30 years, though cellulose may settle over time and require reapplication.
Can blown-in insulation be added over old insulation?
Yes, if the existing insulation is dry, pest-free, and not compressed.
How is blown-in insulation different from batt insulation?
Blown-in provides more thorough cavity coverage and is better for irregular spaces. Batts work well for open wall or floor joists.
Will blown-in insulation stop drafts?
No. It slows air movement but does not act as an air barrier. Air sealing is needed in conjunction.
Service Options for Fort Walton Homes
Prestige Insulation Solutions offers several services relevant to blown-in insulation selection:
- Blown-In Insulation: Loose-fill material installed in attics and walls to improve thermal coverage.
- Spray Foam Insulation: Closed-cell and open-cell foam to provide air sealing and high R-value per inch.
- Insulation Removal: Safe extraction of old, damaged, or contaminated materials before new installation.
- Roof Insulation: Application of insulation in sloped or flat roof structures to improve heat deflection.
Final Thoughts on Making the Right Choice
Blown-in insulation offers strong retrofit value and full cavity coverage for Fort Walton homes, especially in older structures. The trade-off lies in limited air sealing and potential settling in humid conditions. Pre-inspection and paired air-sealing strategies are key to achieving consistent thermal performance.
Evaluate attic access, roof condition, ventilation, and building codes before making a decision. Compare against other insulation types based on climate-specific performance rather than generic specs.
Contact for Fort Walton Projects
To discuss whether blown-in insulation is the right fit for your home, contact Prestige Insulation Solutions. For questions, scheduling, or assessments, reach out by phone at (850) 429-4969 or email at [email protected].
Questions That Often Come Up After Installation
How do I know if the insulation is still effective?
Measure attic depth periodically and check for cold spots or high energy bills.
Can I walk on blown-in insulation during maintenance?
Only if walkway boards are installed. Otherwise, walking compresses the insulation and reduces performance.
Does it attract mold?
Not directly. Moisture intrusion or lack of ventilation creates conditions for mold regardless of insulation type.
Will blown-in insulation affect HVAC performance?
Yes. Better insulation reduces HVAC runtime, improves efficiency, and stabilizes indoor temperatures.
Can I install more insulation later?
Yes. Additional layers can be applied, assuming proper ventilation and attic access.